Local mask manufacturer Detmold Group is on track to produce one million life-saving face masks per day. But these single-use polypropylene-based shields have a much longer life than their initial use.
The lifecycle of a face mask
SPECIAL REPORT: COVID-19 ADELAIDE
The famous dancing plastic bag scene from American Beauty reminds some YouTube commenters of how “beauty lies in the most unexpected of places”.
The clip reminds CityMag of how many disposable face masks we’ve seen littered on the ground since COVID-19 hit (read: a lot).
When the global pandemic became a reality, sustainable practices went out the window. KeepCups were banned in cafés to limit the spread of the virus, and donning a pair of single-use gloves in the supermarket became encouraged.
So, when South Australian-based paper and board manufacturing company Detmold Group won a State Government contract to produce millions of much-needed respirator and surgical masks for health care workers in March, we wondered what impact this would have on the environment.
An SA Health document says the deal was to provide a “sustainable supply chain solution” to the local impacts caused by the global shortage of respirators.
The company has since shipped out the first 2,700 of its newly minted D95+ respirator masks to metropolitan hospitals from its Brompton manufacturing plant.
Detmold says on its website it’s committed to environmentally friendly manufacturing practices, and examines the sustainability of its products every step of production.
Tom Lunn from Detmold Group says the new masks were designed foremost to protect the healthcare worker, but they’re always looking at ways to make products environmentally friendly.
“It’s very much designed with the health of the clinician in mind,” Tom says.
“The D95+, that respirator, is absolutely trying to create an air seal so that there are no particles in the atmosphere entering around the sides of that mask, to protect that health worker.
“We make it by combining, typically, four layers of various specifications of the non-woven polypropylene. One is hygroscopic, so it stops blood entering or fluids entering.
“The one on the inside is the opposite – it actually absorbs some moisture so that your breath and condensation don’t build up.
“Then you have the active layers of filtration in between, which is stopping the bacteria from passing, so it’s actually a bacterial barrier.”
The D95+ masks are single-use, Tom says, but the longevity of the mask is determined by the type of work done by the health worker. Those working in intensive care or an infectious disease department need a new mask for every patient they see. In lower-risk areas like radiology, however, the health worker may be able to wear a single mask for an entire shift.
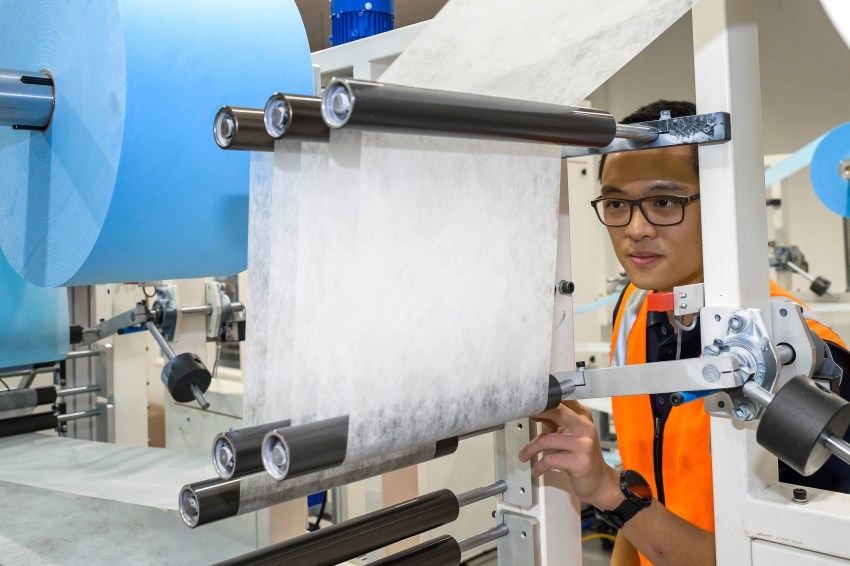
Above: Detmold engineer Darren Tan checks the raw material; Right: The finished product
Single-use medical equipment, of course, isn’t new.
A range of surgical tools can only be used once, to limit cross-contamination or re-infection.
Tools can be sterilised and re-used, but that depends on the manufacturer’s instructions, says SA Health.
For now, Detmold is working within the parameters of what it can do: to ensure the plastic-based masks keep the wearer safe, and are at least disposed of adequately.
“It’s still early days. It’s only been 14 weeks since the project started,” Tom says.
“Our focus, in terms of the sustainability of the masks, is really to partner with Med-X.
“Med-X collects streams of medical waste and their focus is really to find recycling options for all of those waste streams.”
Tom says if these masks are sent to landfill, they would deteriorate into microplastics. They are in no way biodegradable and need to be recycled in a specific industrial process to reclaim the materials.
The company is currently in talks with technology companies and universities to explore renewable-based materials, like hemp and paper.
But even the stock-standard store-bought masks are made from this non-woven polypropylene.
“The same lifecycle issues apply.”