With South Australia currently in a housing crisis, architect and business owner Justin Cucchiarelli observes how the construction industry is navigating this period of growth, inflation and escalation.
Built form: What could get housing construction moving again
The state’s housing crisis is a complex issue, with some misunderstanding of who is benefiting and profiting from the current market.
The pandemic instigated a wave of uncertainty in the construction sector. Material shortages and cost increases, associated transport issues and people contracting COVID on-site led to project delays and increased costs.
While material shortages and cost increases have somewhat stabilised post-pandemic, construction delays are much harder to resolve due to the complicated nature of the issue.
While tradespeople enjoy high demand and command premium rates, builders – particularly, residential builders – are struggling to break-even.
What many don’t recognise is there are key differences between commercial builders and residential builders.
Residential builders have less on-site builder supervision and less stringent occupational health and safety requirements than their commercial counterparts. Their contracts often exclude provisions for delays, leaving owners with little recourse when construction durations extend. They work on fixed-price contracts, but often tender their trades as they progress, meaning they are susceptible to price increases.
Read the entire back catalogue of Studio Nine’s design column here.
While homeowners feel frustrated by extended construction durations, builders share those frustrations. A builder’s profitability is dependent on timely project completion. Prolonged construction periods result in increased on-site costs and potential rises in materials and labour. Pre-pandemic, house builds generally took around eight months, but today they can take up to almost 24 months.
As a business owner, I understand the predicament builders face. Qattro’s Managing recently said, “The reality is that selling something under contract for $1, that costs $1.20 to produce can only go on for so long”. Builders are caught in a precarious balancing act, selling something lower than it costs to produce.
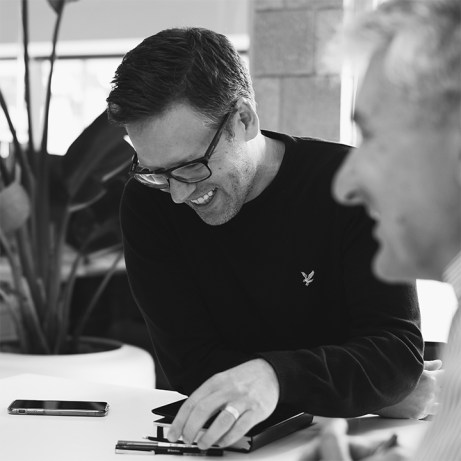
Justin Cucchiarelli, Studio Nine Architects Director.
The consequence of a builder going into administration has multiple flow on effects. Clients face the daunting prospect of finding alternative solutions, which involves additional time, financial implications and stress. The builder’s employees will be made redundant and may not be paid all their entitlements, and the builder’s subcontractors and suppliers may be left with outstanding debts.
The trades are taking on more work than they can complete in a timely manner and are spread too thin. The shortage of tradespeople resulting in extended construction times and inflated labour costs, requires immediate attention. There is no silver bullet. Sustainable solutions require long-term planning and coordination among peak industry bodies – which appears to be lacking at present.
Short-term solutions could involve attracting interstate and overseas workers. However, there needs to be structural changes around federal immigration laws to incentivise both workers and employers through visas and pathways to residency. With so many large infrastructures in the pipeline in SA, we could be attracting skilled tradespeople from overseas to work on these megaprojects for multiple years, with the guarantee of residency at completion.
There are currently minimal incentives to finish apprenticeships. Improving apprentice wages through government subsidies, both to the apprentice and employer, could assist in ensuring more apprentices complete their training and go on to long careers within the industry.
The other major opportunity is to attract more females to trades and the construction industry, which requires better conditions onsite and removing the stigma of a male-dominated industry.
Our existing university-centric schooling model doesn’t do enough to promote trade-based occupations and the benefits of learning a trade. I know some schools do not even have trades at their career expos, minimising the opportunities for understanding career pathways.
European education models, which provide different schooling types that differentiate students who will head to trade school versus those who will go to university, should be further explored. The new technical colleges for year nine and 10 students currently being delivered by the state government will hopefully provide a consistent pipeline of new tradespeople.
The road ahead requires a concerted effort to bolster trades, innovate contracts and enhance the industry’s efficiency and accountability. There’s no simple solution – there’s layers of issues. But the starting point is greater collaboration between industry, state and federal government departments and peak bodies.