With its constant growth and a new international contract to supply systems for driverless cars, SA shock absorber company Supashock is proving that reports of local manufacturing’s death are greatly exaggerated.
Smoothing the path to growth
Oscar Fiorinotto has always been very good at engineering suspension for race cars.
He’s been in demand – working across the US, Europe, Sydney, Melbourne, and South Australia for companies that realised his ability to stabilise a car at high speed around a corner could be the difference between winning and losing.
But still, when he stepped out on his own, it was an uphill battle. After all, in the world of Formula One, Australians don’t really rate a mention.
“I started the business in about 2005 and then spent seven years developing the product so it was right. It was just me and two others, but mostly me,” says Oscar.
“And in 2012, we took it to Germany – we’d built the world’s lightest Formula One shock absorber at the time. I did a lot of door knocking and that was really hard. One of the interesting things was when I was approaching these teams, they were saying, ‘what can an Australian teach me?’
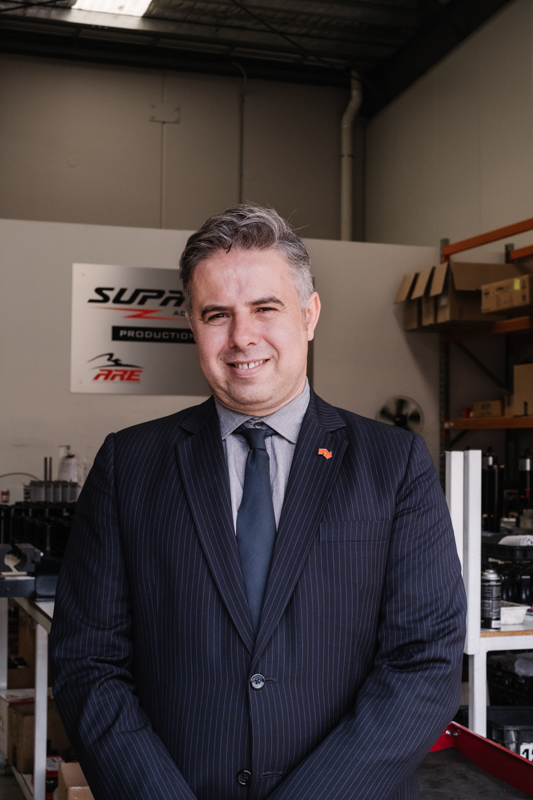
Supashock CEO Oscar Fiorinotto
“But in the very first test in East Germany, they were 0.4 of a second quicker with a Supashock product. In racing, that’s like a lifetime. This is a team that was qualifying 18th at the time, and with the first use of Supashock we qualified second.”
This was how Supashock’s story began – with a reputation built purely on the back of Oscar’s ability to create something that was better than anything else in the world.
And that is how the business has continued to grow.
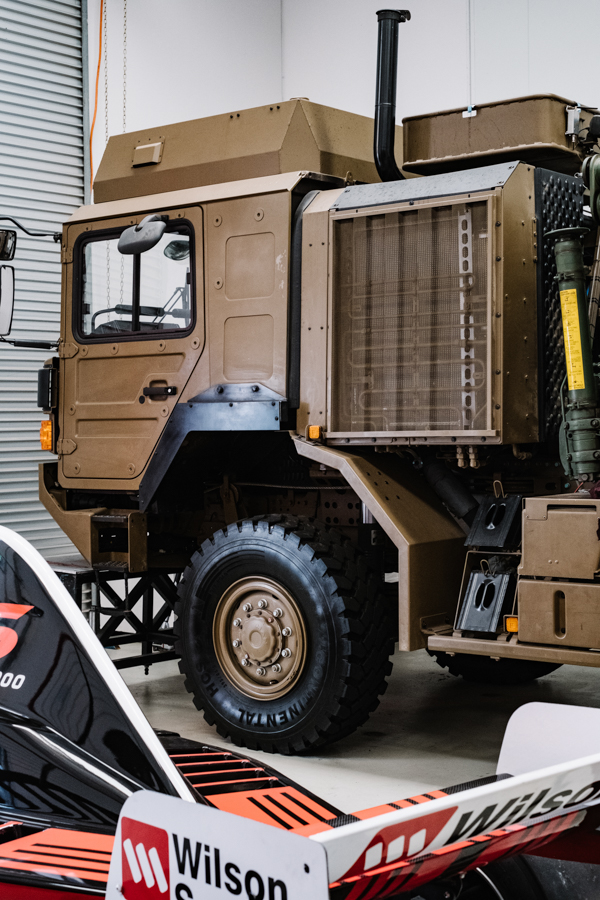
Supashock has built suspension systems for both of these very different vehicles
In the past six years, Supashock has diversified greatly. No longer does the business make suspension systems just for racing – these days, the team of about 30 people design, engineer, and manufacture for everything from army tanks in Germany to the latest Holden Commodore.
The company’s latest contract will see them enter the US market as the creator of suspension systems for driverless cars. Engineering the right solution for this whole new mode of transport has been a challenge Oscar and his team tackled enthusiastically.
“Basically what it does is keep a nice beautiful ride – so the ride is really nice and soft, but without the body roll,” says Oscar.
“With an autonomous vehicle, it’s quite likely some of the occupants may not be facing the direction of the vehicle’s travel and the suspension plays a big role in potential motion sickness – so we’ve been working really hard on that and we have a system now that is quite mature.”
This new American contract, along with a significant investment from German company Rheinmetall in 2017, is helping to fuel growth at Supashock, which will likely have about 80 employees by 2020.
When CityMag visits, the business is also half way through moving to new, larger premises. The Magill facility is no longer big enough to accommodate Supashock’s engineering, electronics, vehicle dynamics, testing, verification, manufacturing, and production teams.
While Oscar will retain the space at Magill as an office and showroom, most of Supashock’s employees are relocating to the new site in Edinburgh Park. It’s a move that’s highly symbolic of the company’s strong movement against the manufacturing downturn that’s followed the demise of the local automotive industry.
“One of the ironic things is it’s where one of our competitors were assembling the Holden suspension and they’ve closed down and we’re taking it over,” says Oscar.
Oscar credits Supashock’s resilience to its early diversification – “if you rely on one industry to prop your business, you’re in trouble,” he says – but adds that the ability to diversify is only possible if you foster the right talent.
As CEO, Oscar believes Supashock’s team is its main asset. The company’s ability to beat out competition in American and Europe, and to create suspension so desirable that Holden still buys it even though they’re manufacturing offshore, is rooted in the minds of its employees.
“My vision and passion has always been to take what I know, develop it, and then actually provide opportunity – just like I had opportunity out of university – for younger people to actually come in and assist in the development,” says Oscar.
“Their career paths bring new products to life.
“And that’s what the whole business has been about, so we have engagements with Flinders University and University of Adelaide – intern programs where those students have the ability to not only come out of university and be successful but to come out of university and do some real engineering, and that’s rare today.”
Phillip Kuys – Supashock’s Engineering and Quality manager – is a living embodiment of how this process can play out.
From university, Phillip came to Supashock with little experience in suspension. But very quickly, he was in charge of an award-winning project.
“When I started I was working on some pretty low-level documentation, which is how I wrapped my head around how shock absorbers actually work,” says Phillip.

Manufacturing of the high-end components is a manual process
“The step from there was to designing my own suspension system for the HSV GTSR W1, so I designed that system with a lot of input from Oscar. That’s the Commodore – the latest Commodore, and it’s a very high-performance car. It won Driver’s Car of the Year [in 2017].”
Fostering the aptitude of the Supashock team is also made possible by keeping all parts of the production process in-house.
Rather than simply designing a suspension system and outsourcing its creation, Supashock does everything from writing the code that controls the system’s response to different situations, to physically creating and assembling the parts.
In doing this, Oscar says room is created for new thinking and continuous improvement.
“We have a lot of extremely talented people in manufacturing – and we manufacture everything, everything here is done from scratch,” says Oscar.
“We’re developing and it doesn’t make sense to send stuff away when we’re constantly evolving what we’re doing and how we’re doing it. We’re looking always at new ways to try and bring things to the market.”
Not only does this ground-up methodology spread greater knowledge throughout the Supashock staff base, Oscar is also making sure it grows capacity more broadly in the South Australian industry.
“We try, where possible, to really maximise South Australian suppliers,” he says.
“In some aspects, I’ve coached suppliers. Not every supplier is going to be at your standard but we try to look at bringing them with you instead of demanding unrealistic goals. That’s important in terms of bringing the supply chain here where possible.
“And there are also times where we have to develop technology because no one else can do it. That’s interesting because it creates additional capability and if you do it really well you become known in the industry and there’s a demand.”
Oscar is not originally from South Australia. He came here back when he was working for companies on race car suspension, and saw a place with the potential to house the kind of business he wanted to run.
“I call myself South Australian. I’ve worked all around the world but this is what I call home,” he says.
His belief in the state and its people is paying personal dividends as his business grows. But, equally, it’s paying off for South Australia as Supashock does its part to reverse the tide of the brain drain, and shine some light in a formerly gloomy advanced manufacturing landscape.